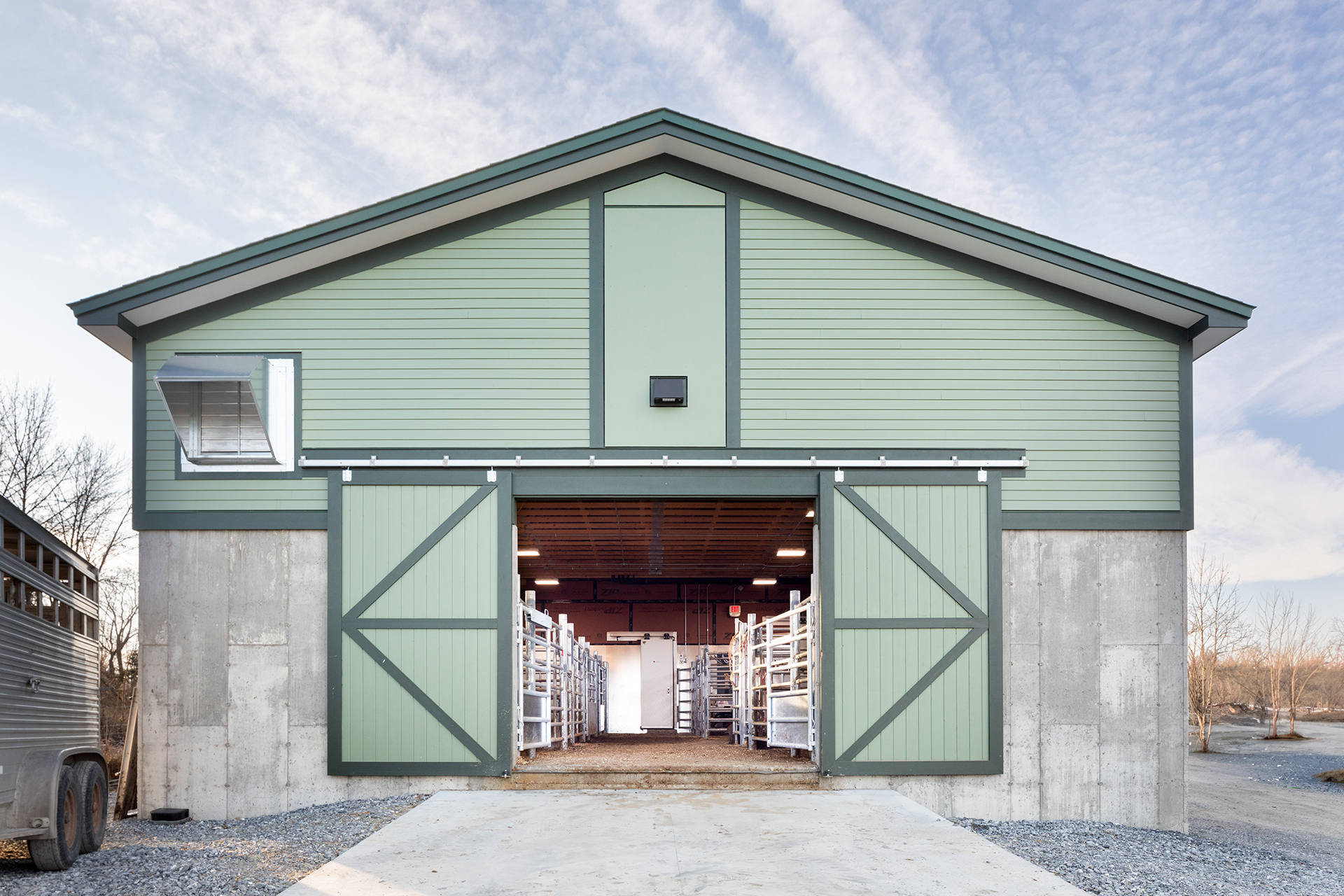
Project Details:
Ferrisburgh, VT
Food & Beverage
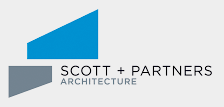
Project Overview:
The modernization and expansion of an important agricultural business located in Ferrisburgh, VT.
VT Livestock currently processes beef, pigs, and sheep for both commercial and residential customers, an incredibly important service for Vermont’s agricultural community. A multi-phased occupied renovation, modernization, and expansion totaling approximately 12,000sf is vastly expanding VT Livestock’s processing capacity, increasing value-added product manufacturing systems, and improving energy efficiency.
Project scope to achieve these goals includes new cooler and freezer panels with gravity fed rail hanging system, as well as state-of-the-art pneumatic slaughtering equipment. This expanded process and cooler storage area for larger process capability will quadruple the number of animals able to be processed. Rehabilitation and envelope upgrades to the existing ice barn will greatly increase thermal values and improve energy efficiency.
A Challenge:
The multi-phased expansion and renovation of the Vermont Livestock Slaughter & Processing Company (VTLS) presented very specific challenges outside of the typical renovation of an occupied business. The VTLS facility is a USDA-inspected slaughterhouse regulated and inspected by the government under federal law, with a USDA inspector on-site at all times during the facility’s operation. Livestock must be slaughtered and processed under inspection and according to specific guidelines. The process of maintaining the operation of a business during construction is a challenge we regularly execute successfully. Constructing in and around an operating USDA-inspected slaughterhouse presented new and unique challenges — in particular, adhering to stringent requirements to ensure environmental and sanitary conditions were maintained throughout the duration of the project.
Our Solution:
A detailed understanding of the facility’s operation and a clear understanding of the required regulatory and inspection process was the foundation for developing a thorough construction phasing plan. Each phase was carefully developed and reviewed well in advance to understand how the construction effort would remain isolated from the facility’s operation. This detailed plan was then reviewed with the on-site inspector and adjusted accordingly. The location and construction of animal holding enclosures, the coordination of mechanical system upgrades and replacements, and the sequencing of the new cooler/freezer system installations, for example, all needed to be coordinated within USDA’s guidelines and the process operation of the facility. Paramount to a smooth implementation of the planning work was clear and constant communication with the project team, and the ability to be flexible and adjust to changing conditions and operations within the facility.
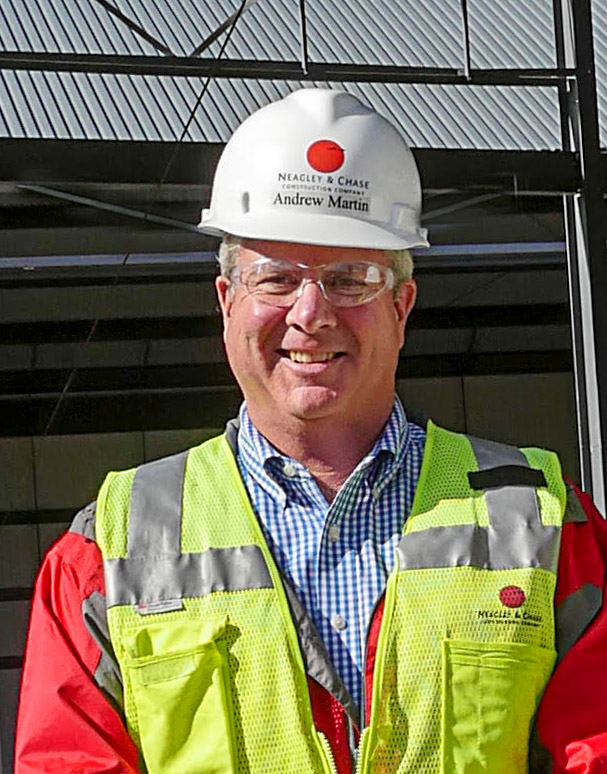
CEO