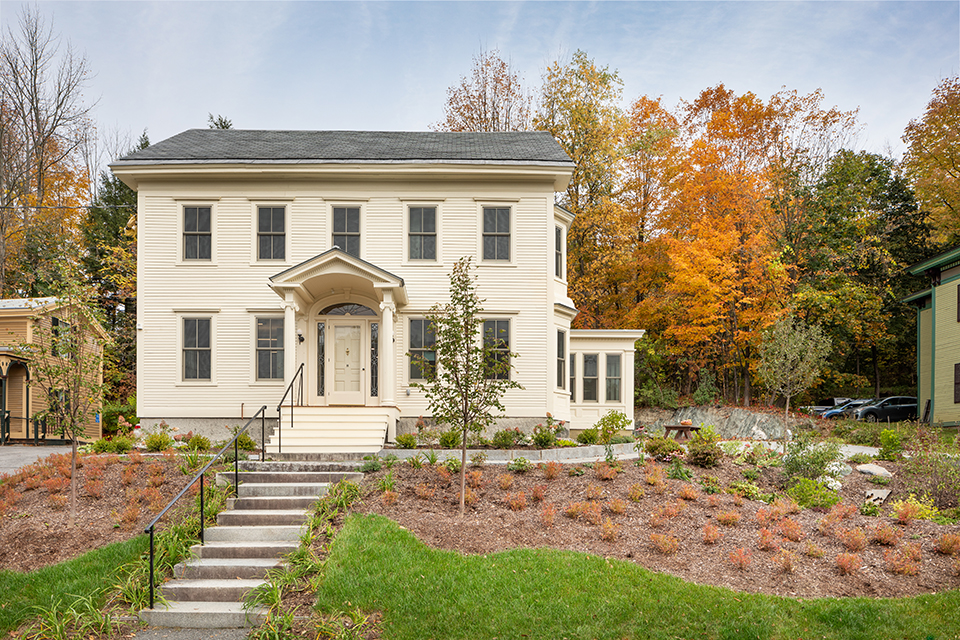
Project Details:
Montpelier, VT
Office/Commercial
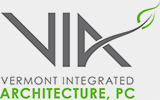
Project Overview:
Historic Restoration & Adaptation of the Vermont Natural Resources Council (VNRC) Headquarters in Montpelier, VT.
Project included a complete rehabilitation of a beautiful Federal Style residence built a few doors down from the State House in the late 1800’s.
The scope of work included full thermal envelope and window upgrades, complete MEP systems replacement, site improvements, reconfiguration of spaces, universal access features, and updated finishes throughout.
The project’s sustainability goals included Net Zero Energy and Low Embodied Carbon.
A Challenge:
Here was a historic structure where robust high-performance envelope criteria were set to ensure the project’s sustainability goals are met without touching the exterior of the building. Many of today’s retrofit envelope solutions tackle air barrier upgrades and thermal upgrades from the outside of the building, removing existing siding and installing continuous air barriers and insulation before finally re-siding. A common and successful strategy for many, but VNRC needed the historic siding, details, and trim to remain in place meaning all improvements needed to be made from the interior. The realities of field stone foundations, historic framing, materials, millwork, and details all combined to present a unique challenge to achieving high performance.
Our Solution:
NCC worked closely with the design team during preconstruction to identify the tricky spots. Among many contenders, the standouts included the field stone foundation wall-to-sill beam to first-floor framing transition, the first-floor to second-floor framing and substrate, and the top plate to roof framing intersection. The next step was the review the constructability of the new wall section at each of these areas. The proposed solution included the removal of existing interior finishes, new framing to provide additional bay depth, smart air/vapor barrier, dense pack insulation, and new interior finishes. Ensuring strong terminations where continuity was not possible, closely monitoring installation, and interim smoke and fog testing, were key quality control measures. The result is an envelope that is 72 percent less leaky than before the renovation, allows a net zero mechanical approach, increases occupant comfort, and ensures the building’s resiliency.